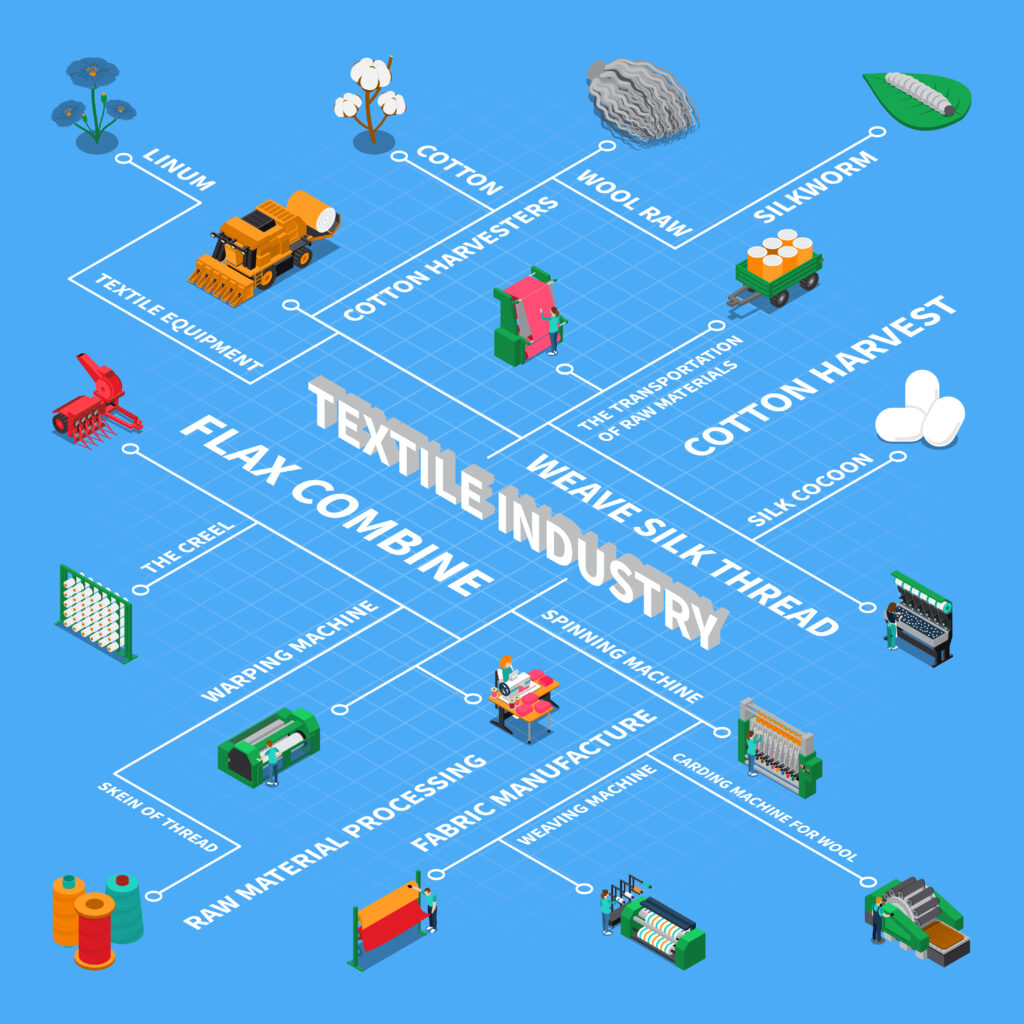
📊 Value Stream Mapping (VSM): A Lean Manufacturing Power Tool
In the ever-evolving world of manufacturing, staying competitive means cutting waste, optimizing processes, and delivering value faster than ever. Lean Manufacturing offers powerful methodologies to achieve these goals—and one of its most essential tools is Value Stream Mapping (VSM).
But what exactly is VSM? How does it work, and why should you care?
This blog dives deep into what VSM is, how it’s used, and how it can drive massive improvements in your operations.
🧭 What is Value Stream Mapping?
Value Stream Mapping is a visual tool used in Lean Manufacturing to analyze, design, and improve the flow of materials and information required to bring a product or service to the customer.
It helps organizations:
- Visualize the entire process flow
- Identify waste (muda) in the system
- Understand the relationship between process steps
- Find opportunities for continuous improvement
Key Concepts:
- Value Stream : All the actions (both value-adding and non-value-adding) required to produce a product or service.
- Current State Map : A snapshot of how your process works today.
- Future State Map : A redesigned version of the process with improvements applied.
🏭 VSM and Lean Manufacturing
Lean Manufacturing is all about maximizing customer value while minimizing waste. VSM fits perfectly into this philosophy by offering a structured method to spot inefficiencies in your processes.
VSM Helps Identify:
- The 8 Wastes of Lean (Transport, Inventory, Motion, Waiting, Overproduction, Over processing, Defects, and Unused Talent)
- Bottlenecks and delays
- Overlaps or gaps in information flow
- Poor communication between departments
🛠️ How to Create a Value Stream Map (Step-by-Step)
Creating a VSM might seem complex, but it can be broken down into clear steps:
1. Select the Product or Process Family
Focus on a specific product or product family that flows through similar processes.
2. Map the Current State
Observe and record:
- Each step in the process
- Cycle time, lead time, uptime
- Inventory between steps
- Information flow
Use standard symbols for processes, inventory, material flow, and information flow.
3. Identify Waste and Opportunities
Highlight non-value-adding activities. Look for long lead times, excessive inventory, or rework.
4. Design the Future State Map
Reimagine the process with improvements:
- Eliminate or reduce waste
- Improve flow and communication
- Add pull systems or kanban where applicable
5. Create an Action Plan
List all the steps needed to move from the current state to the future state. Assign responsibilities and timelines.
6. Implement and Review
Carry out the plan, track results, and adjust where needed. Continuous improvement is key!
🧩 VSM Symbols and Elements
Here are some common VSM symbols you’ll use:
Symbol | Meaning |
---|---|
🏭 | Process Step |
📦 | Inventory |
↔️ | Material Flow |
📡 | Information Flow |
⏱️ | Lead Time / Cycle Time |
🔁 | Push / Pull Arrows |
Learning to use these symbols consistently makes your maps clearer and more effective.
📈 Benefits of Value Stream Mapping
- Clarity : Provides a clear, shared understanding of processes.
- Efficiency : Identifies and removes bottlenecks and delays.
- Customer Focus : Aligns operations with customer needs.
- Engagement : Encourages cross-functional collaboration.
- Continuous Improvement : Becomes the foundation for kaizen events and lean projects.
🔄 VSM in Practice : Real-World Example
Let’s say you’re producing automotive parts. A VSM of your assembly line might reveal:
- Long idle time between welding and painting
- Large batches sitting in staging areas
- Delays due to missing parts or miscommunication
After mapping:
- You shift to smaller batch sizes (lean flow)
- Introduce kanban to pull parts only when needed
- Reorganize layout for better flow
Result? Lead time drops by 30%, inventory costs decrease, and output improves—all thanks to insights from VSM.
🧠 Tips for Successful VSM Implementation
- Get the team involved : Include operators, supervisors, and support staff.
- Go to Gemba : Observe the actual place where work happens.
- Don’t overcomplicate : Focus on clarity and key metrics.
- Follow up : VSM is a tool, not a one-time fix.
🔚 Conclusion
Value Stream Mapping is more than a flowchart—it’s a strategic tool that reveals inefficiencies, empowers teams, and drives continuous improvement in Lean Manufacturing.
Whether you’re just starting your Lean journey or looking for your next breakthrough, VSM can light the way.
✅ Ready to transform your processes with Value Stream Mapping? Start by mapping one product line today—or reach out and let’s explore how Lean thinking can drive results in your organization!