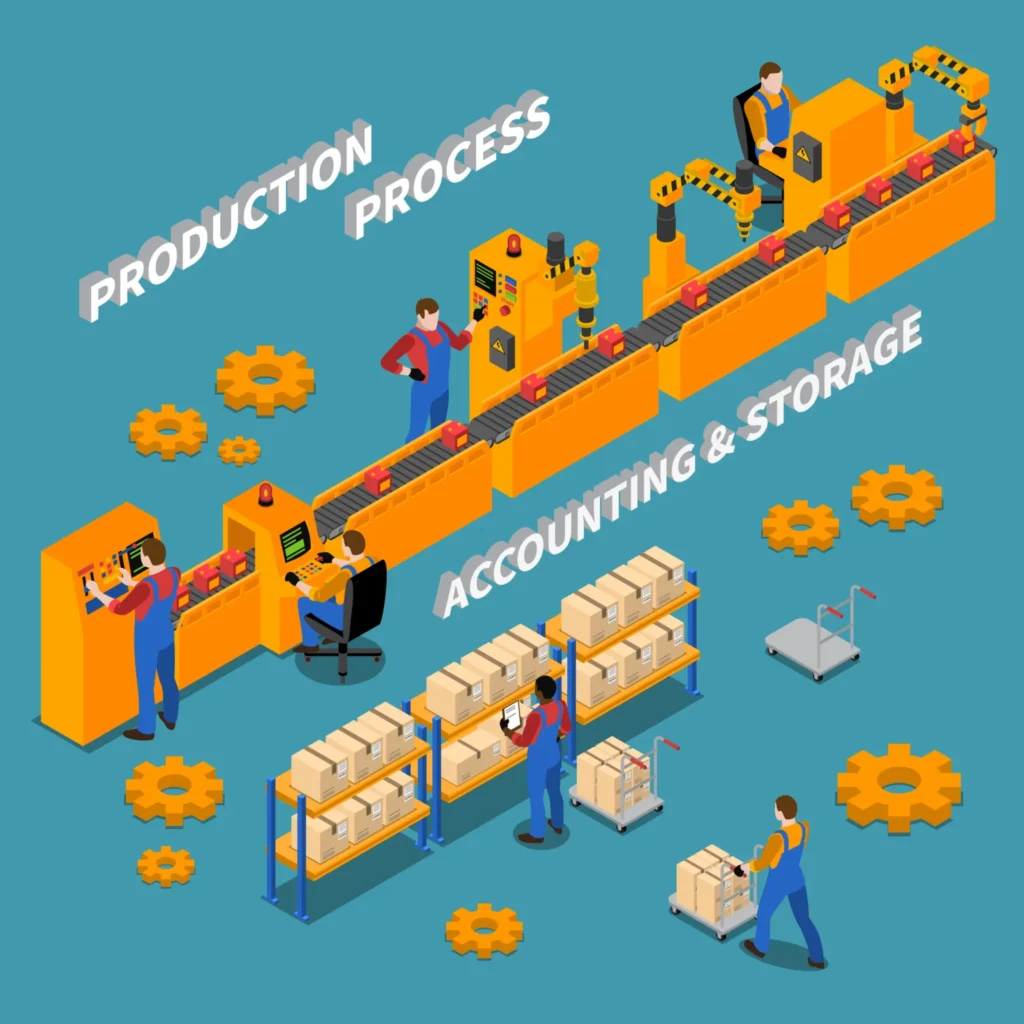
In Lean manufacturing, TIMWOOD represents seven types of waste that should be minimized or eliminated to improve efficiency and productivity. Here are each of the TIMWOOD wastes with examples:
- Transportation:
- Example: Moving materials or products between workstations or locations unnecessarily. For instance, transferring components from one side of the factory to the other when they could be stored closer to where they’re needed.
- Inventory:
- Example: Holding excessive amounts of raw materials, work-in-progress (WIP), or finished goods. This ties up capital and space and increases the risk of obsolescence. For example, a company ordering and storing a year’s worth of inventory when it only needs a few months’ worth.
- Motion:
- Example: Unnecessary movement of workers or equipment. This includes reaching for tools, walking long distances to retrieve materials, or repeatedly adjusting equipment. An example could be a worker having to walk to a different floor to access a printer repeatedly throughout the day.
- Waiting:
- Example: Idle time for workers or equipment due to delays in the production process. This can include waiting for materials, instructions, equipment setup, or quality checks. For instance, a machine operator waiting for the previous shift to finish so they can start their work.
- Overproduction:
- Example: Producing more than what is needed or producing items before they are required. This leads to excess inventory, tying up resources and increasing the risk of waste. An example could be a bakery producing more bread than there is demand for, leading to stale product or waste.
- Overprocessing:
- Example: Performing unnecessary or redundant steps in a process that do not add value to the final product. This can include extra inspections, paperwork, or additional processing steps. For example, conducting multiple quality checks on a product when one thorough check would suffice.
- Defects:
- Example: Errors, rework, or defects that require resources to fix or result in scrapped products. This includes defects in materials, workmanship, or design. For instance, a manufacturer having to rework a batch of products because they were assembled incorrectly due to a design flaw.
By identifying and eliminating these types of waste, organizations can streamline their processes, reduce costs, improve quality, and enhance customer satisfaction in Lean manufacturing.